

Without setting a wall thickness, a 3D printer has no information about how thick or how thin it is supposed to print your part. In order to make your Cinema 4D model printable, you need to ensure that each and every surface of your model has a wall thickness. 7: Wall Thickness – Making Sure Your Walls Are Printable Sometimes this extra geometry is hard to spot since it is located inside the model (see step 5 of this tutorial). This will highlight any unwanted extra faces or edges that might cause problems. Next thing you should do is check the “ Non Manifold” box. This will show you the “holes” in the mesh of your models, which keep them from being watertight.Ĭheck if your model will be 3D printable. Enable “ Mesh Check” and “ Boundary Edges” and uncheck all other options. Open the Attribute Manager and then choose Mode – Modeling – Mesh Checking Tab. You can identify issues with watertightness by using Mesh Checking. Luckily for us, Cinema 4D has a tool that shows us exactly where those holes are. You can clearly see that there is a big gap in its surface. The design below is an example of a model that is not watertight.
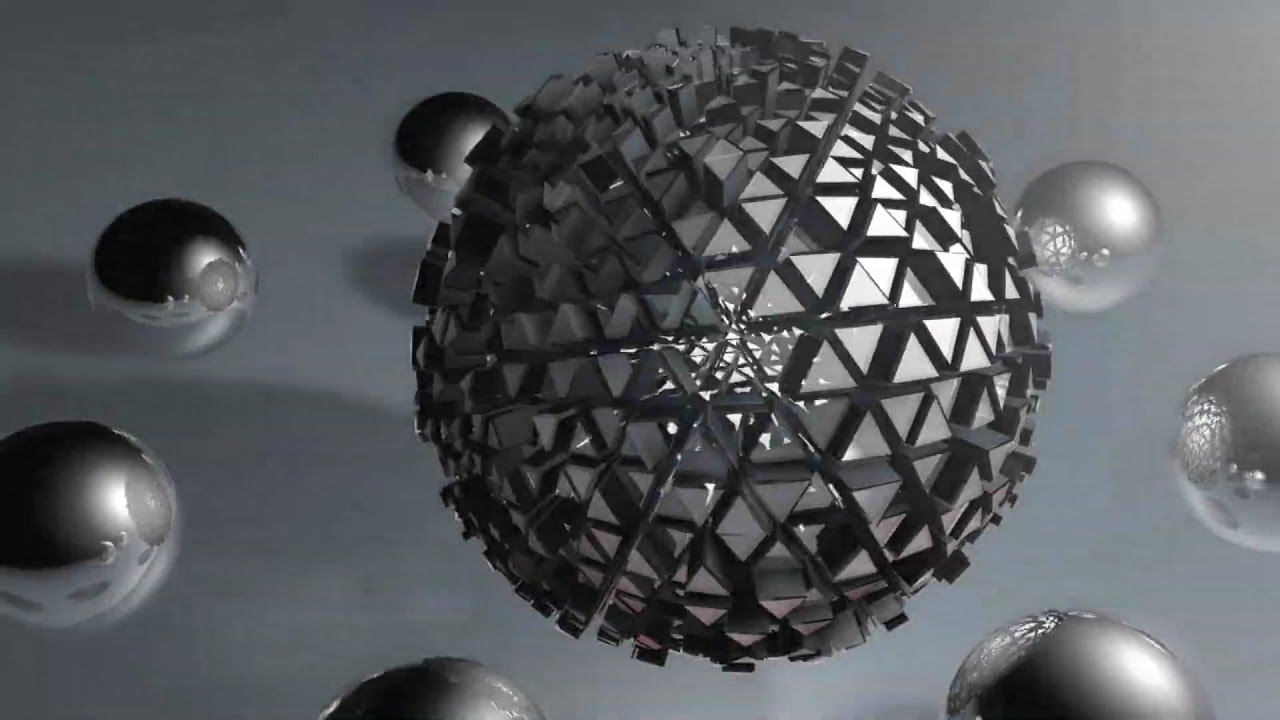
Ask yourself the question: if I were to put water inside my model, would it flow out? If that’s the case then you need to find those holes and close them. For example, your model needs to be watertight. This is where key geometry issues come into play. 6: Making your Model Watertight & ManifoldĬreating a design for 3D printing means that your Cinema 4D model has to be able to exist in the real world. She has recently moved from working in post-production to branding and packaging.Merging unprintable objects (left) together for 3D printing (right) with Magic Merge. Experiment with various strengths of blur, as well as increasing and decreasing the contrast between black and white on your map.įrankie is a 3D artist and visualiser in London.
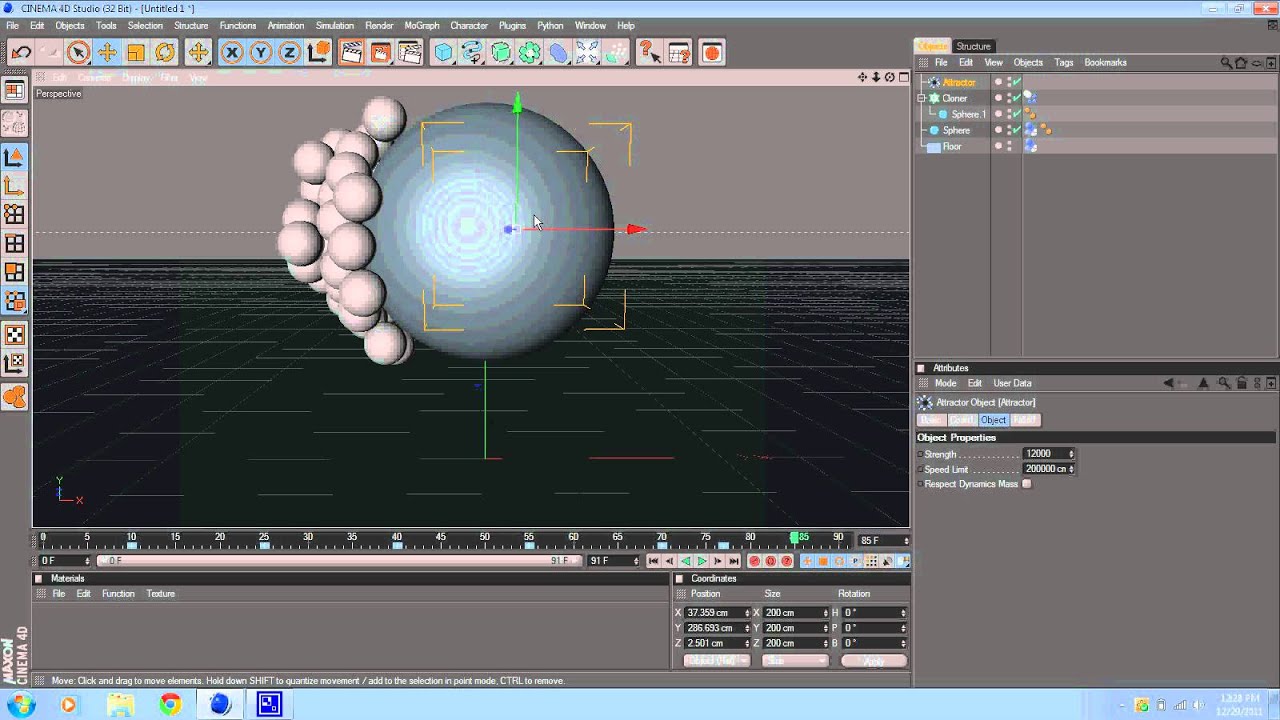
Bonus tip: Add a blur to your displacementīy blurring the edges of your displacement map slightly, you can give your texture a much smoother embossing/debossing effect. I’ve found this works the best by giving you a live preview to see your displacement position, height and resolution, and letting you keep your mesh low resolution, which does not effect the quality of your displacement. Then you can control your displacement as normal through your material, like in the initial route. This means the Displacer Deformer will mirror the displacement created by the Displacement Material channel. In your Displacer, click Object and tick Emulation. Next, create a Null and a Displacer Deformer and place both the object and Displacement Deformer into the Null.
CINEMA 4D SPHERE MESH PLUS
So you have your object with your base texture on, then your same texture, plus the displacement applied to your selected faces only. Add a selection tag to the faces you want to apply your displacement onto and add your material here. Apply your displacement as normal through your displacement channel in your second material. The third and final way I’ve created a displacement on an object is a combination of the two approaches above.Ĭreate your texture for your object, and duplicate it. The issue I have with this method is that you have to subdivide your object a crazy amount to get smooth high-resolution embossing, which slows down render times and can be a real pain if you need to alter your object at a later time. So this will take your texture and use whichever channel you have put in your displacement map, in this case we used the Colour channel. Create a Displacer Deformer and make it a child of the object you’re displacing, click Shading in your Attribute manager, set your Channel to Colour, and in your Texture Tag, drag and drop your newly made texture from your Null object in there. Create a Null object and put this new material onto the Null.
